Maintaining
Ageing Aircraft
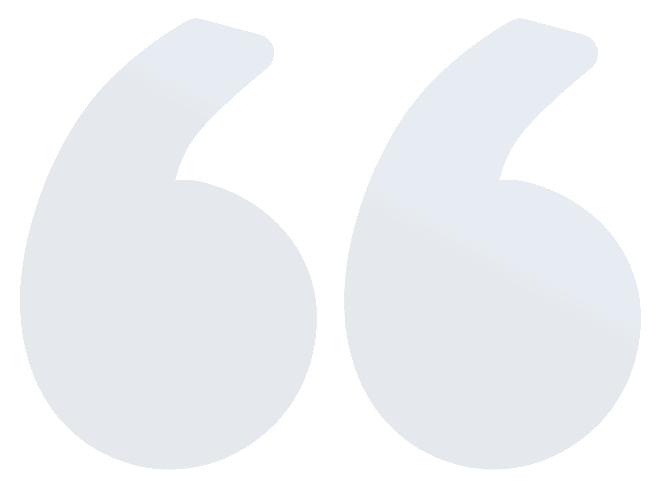
All aircraft whether general aviation, business jets, commercial airliners or defence aircraft will begin the ageing process from the day they are first flown.
Hallmarks of an ageing aircraft can include corrosion, airframe fatigue, electrical wiring failure or other component failure due to wear out. There are many complex variables which contribute to ageing aircraft. The useful lifespan of aircraft is often determined by:
- Aircraft type
- The environment the aircraft is flown and stored in
- How often the aircraft is flown
- How frequently the aircraft is maintained
- Availability of replacement parts and components
- The products and procedures used in the maintenance process
Develop an Ageing Aircraft Program
A well planned and informed Ageing Aircraft Program can add not just years but often decades to an aircraft’s service life. Properly informed planning and maintenance will save billions or even tens of billions to a large fleet operator, while smaller scale aircraft owners and managers are set to save thousands.
Understanding when specific components are likely to fail is imperative if an operator or owner is motivated to save on unnecessary costs. It will always be more cost effective to plan and replace a component when an aircraft is scheduled for maintenance than to tow an aircraft off the flight line for unscheduled maintenance.
To help inform an ageing Aircraft Program, reliability theory works to mathematically predict failure rates in aviation equipment by utilising statistically gathered parameters for individual components. By having dependable information on the failure rate for each component in a design, a reliability engineer can predict with some confidence the Mean Time Between Failure (MTBF).
Reliability theorists attribute aircraft component failure into two basic types:
Random Failure
- Hidden manufacturing defects
- Unexpected but uncommon causes of component damage
Wear out Failure
- Mechanical wear
- Corrosion
- Fatigue damage
Bathtub Curve
Experienced engineers dealing with ageing aircraft refer to the Bathtub Curve, this plots the average failure rate for a specific design and its many components over a designated period of time. There are three main stages in the Bathtub Curve:
1. Infant Mortality
Statistically, there is usually a high failure rate in the first few weeks or months after an aircraft leaves the production factory. These failures are the result of component defects which were missed during factory testing. This is termed ‘infant mortality’.
2. Active Life
Rates of failure then drastically decrease once production faults have been found. This ‘active life’ phase is commonly defined as the section of time where aircraft exhibit low wear out failure rates. Most failures experienced throughout this period are categorised as random.
3. Wear out Phase
After a designated period of time the components will wear out and corrode. The aircraft therefore enters the ‘wear out phase’ and as a result the failure rate substantially increases.
In the game of elongating the service life of aircraft, it becomes about how to best manage wear out of the various components in the aircraft’s design. A well planned, informed and executed management strategy can see those components nearing wear out replaced in blocks. Thus, avoiding the problem entirely and maintaining the initial design to lengthen the active life phase, potentially indefinitely.
Airframe Corrosion
Airframe corrosion is an unfortunate reality for any aircraft design which contain metal components. The problem can be exacerbated when carbon fibre composites are bonded to metal structures. The vast majority of corrosion within aviation is galvanic. In simple terms, galvanic corrosion results when two dissimilar metals (or metal and conductor – carbon) are bridged by water or another electrolyte which is aptly contaminated. This outplay often arises between microscopic grain boundaries in an alloy component, resulting in tiny pits which tend to expand in size and depth over time.
Corrosion’s damage will mean that the structural strength of parts will be compromised. Corrosion pits often become a stress spot and the location where cracks begin. Alternatively, corrosion on a large area of a part can alter the load bearing design, resulting in the part’s failure.
Corrosion Prevention to Extend Aircraft Service Life
The industry is moving away from chromate surface treatments, instead relying on paint systems which crack and chip in service. This shift leads to greater risks of corrosion manifesting in airframes. Dust particles, insect remnants and water-jet sandblasting on runways will facilitate corrosion to manifest.
To avoid this, the first step is to wash your aircraft regularly with an approved aviation cleaning product. It is important to understand, however, that not all aviation approved cleaning products are created equal. Our Zi-400 HD Aircraft Cleaner is an advanced aerospace cleaning compound. Zi-400 not only provides a robust clean, it has been scientifically proven to deliver powerful corrosion protection and arrest existing corrosion.